Are Deepblue Smarthouse steel prefab homes more affordable than other types of housing?

The general rule of thumb is that prefab construction is cheaper than stick-built homes by an average of AT least 30 percent. Why? Mass-produced materials made-in-China on an assembly line cut down costs because factories buy supplies in bulk. The cost of labor is also less because you don’t have to send carpenters, plumbers, and electricians to individual construction sites. And a faster build time saves money too.
You can expect to pay a starting cost of anywhere from $20 to $40 per square foot, and this price can include appliances, windows, flooring, insulation, wiring for electrical, and doors.It’s also called turnkey prefabricated houses.
Beware, however, that the sticker price of a prefab house isn’t actually how much that house will cost. First, you have to pay for the land to build the house, and you’ll also have to account for soil testing, site surveys, permits, and utility hookups. Preparing the site for construction can be either relatively minor or very expensive depending on the landscape; our prefab home packages don’t include the foundation.
Other costs might include landscaping, driveways, garages, and the cost of a local contractor or builder to finish the home. All of these expenses vary—a plot of land and a contractor just outside Boston could be much more expensive than in rural South Carolina, for example.
How long does it take to build a prefab home?
Depending on the size and finishes of your light steel prefab house, you can build a home in as little as three months. The most prefabricated building can be built in four to six months from start to finish. This is much faster than traditional homes, which average about eight months to build, and in some markets, custom home construction can drag on for years.
Why is it up to 50 percent faster? Building most pieces in a factory limit weather delays makes construction more efficient and creates predictable delivery dates. You also don’t have change orders or as many labor scheduling conflicts. That being said, the prefab permitting process can be lengthy in some regions, adding time to the estimates above.
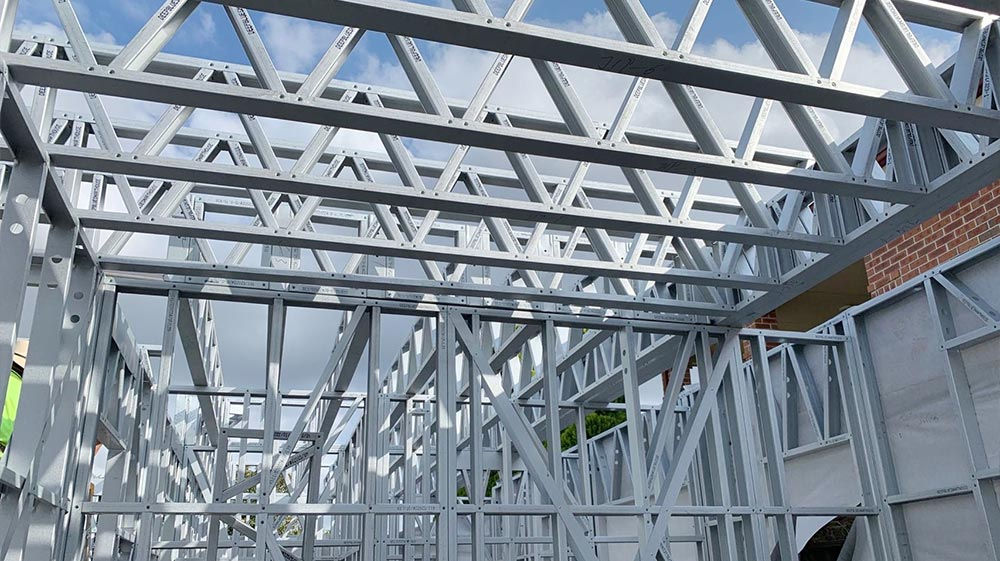
Is Steel prefab more sustainable than traditional homes?
Metal prefab homes are generally considered more eco-friendly than traditional stick homes.
First off, the prefab construction process produces less waste. Instead of having lots of different people delivering materials to a site and producing excess wood, tiles, and trash, factories are more efficient. We are also more likely to reuse or recycle the waste at a factory.
Factory-built homes and parts also have tighter seams than stick homes, which makes heating and air conditioning more efficient. And prefab companies are more geared toward eco-minded packages than many spec home builders; most prefab builders offer energy-efficient appliances, while some include sustainable materials (think: bamboo flooring) and add-on amenities like solar panels and rainwater collection systems.
And in an era of increasing climate challenges, prefab construction scores another point due to its resiliency. Because prefab homes have to withstand being transported by truck, they are often structurally stronger than stick homes, a major plus in regions prone to earthquakes, hurricanes, or high winds.